This article explains differences in techniques of manufacturing rims. So far, there is two main process which affect quality and price of rims in the market.
Forging
Forging is a manufacturing process where metal is shaped by plastic deformation under great pressure into high strength parts.
Casting
The casting process consists of pouring or injecting molten metal into a mold containing a cavity with the desired shape of the casting. Metal casting processes can be classified either by the type of mold or by the pressure used to fill the mold with liquid metal.
Fundamentals of forging
Forging or cold forming are metal forming processes. There is no melting and consequent solidification involved. Plastic deformation produces an increase in the number of dislocations resulting in a higher state of internal stress. Indeed, strain hardening is attributed to the interaction of dislocations with other dislocations and other barriers (such as grain boundaries). Simultaneously, the shape of primary crystals (dendrites) changes after plastic working of the metal. Dendrites are stretched in the direction of metal flow and thus form fibers of increased strength along the direction of flow.
We may distinguish hot working from cold working. Hot working is performed above the re-crystallization temperature; cold-working is performed below it. In hot working strain hardening and distorted grain structure are very rapidly eliminated by the formation of new strain-free grains as the result of re-crystallization. Rapid diffusion at hot working temperatures aids in homogenizing the preform. Initial porosity can also be significantly reduced, eventually completely healed. Metallurgical phenomena such as strain hardening and re-crystallization are important because these changes in structure result in an increase in ductility and toughness over the cast state.
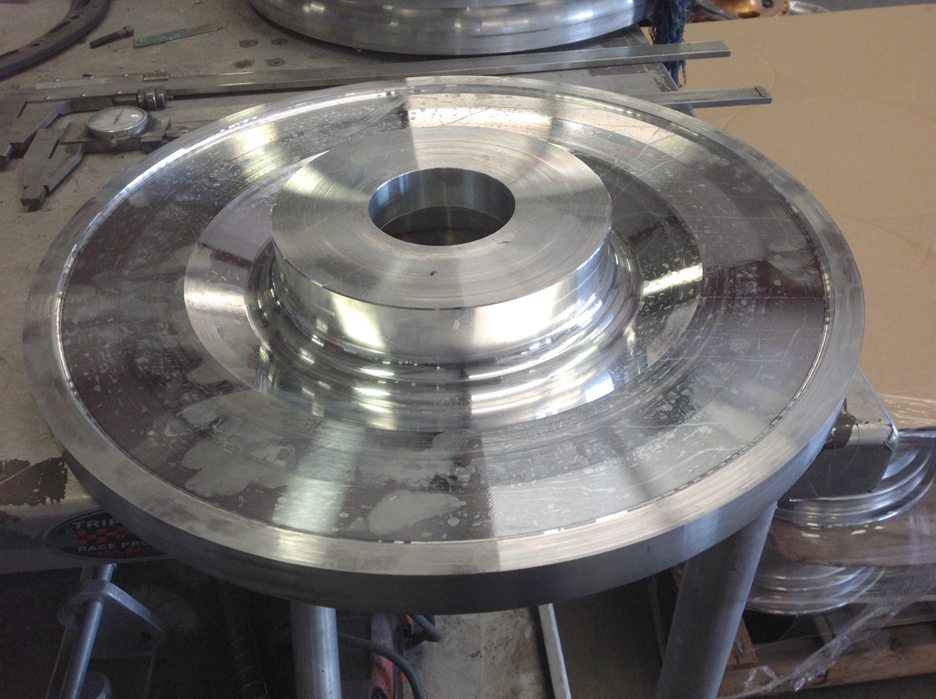
billet
Strength of forging:
- Good Mechanical properties (yield strength, ductility, toughness)
- Reliability (used for critical parts)
- No liquid metal treatment
Weakness of forging:
- Defects : Laps, Die unfill, Die failure, Piping
- Shape limited when undercuts or cored sections are required
- Overall cost usually higher than casting
- Multiple steps often required
Fundamentals of Casting
Casting is a solidification process. Therefore, the micro structure can be finely tuned, such as grain structure, phase transformations and precipitation. However, defects such as shrinkage porosity, cracks and segregation are also intimately linked to solidification. These defects can lead to lower mechanical properties. A subsequent heat treatment is often required to reduce residual stresses and optimize mechanical properties.
During the casting process molten aluminum is either poured or drawn using a vacuum into a mold, where it is formed into the desired wheel shape and allowed to cool. Once the wheel has cooled minor modifications such as drilling and trimming are made, allowing for quick and inexpensive production. While a cast wheel may be easier and less expensive to manufacture, the process of allowing the molten aluminum to solidify leads to porosity, which are essentially inconsistencies in the material structure that unaccounted for can lead to cracking, oxidation, pitting in the finishing, and a reduction in the wheel’s structural integrity. To counteract this deficiency, manufacturers are forced to design with larger tolerances which lead to heavier wheels in order to achieve the desired structural integrity.
Strength of casting:
- Large and complex parts
- High production rate
- Design flexibility
Weakness of casting:
- Defects
- Shrinkage porosity
- Metallic projections
- Cracks, hot tearing, cold shuts
- Laps, oxides
- Misruns, insufficient volume
- Inclusions
- Requires close process control and inspections (porosity may occur)
To summarize, forging yield wheels with higher strength to weight ratio but the tooling due to the multiple steps process and the based alloy are comparatively more expensive than in casting processes. Furthermore, with lighter weight wheels, you will benefit from increased fuel savings, and better acceleration due to less amount of inertial weight at the rotational axis. For those reasons, usually forged wheels are only used for high performance applications.
An important thing to keep in mind is that quality of materials and heat treating may be a more important factor than casting vs. forging in some cases.